What is Inductive Imaging?
Inductive imaging uses special line scanners that deliver images of objects based on their conductivity. They could also be referred to as electromagnetic line scan camera or inductive sensors. These inductive sensors visualize and analyze the electrical and magnetic properties of various materials to detect ferrous and non-ferrous metals. The operating principle is based on how a material interacts with an magnetic AC field.
Sensitivity and Selectivity
Key features that should be considered when choosing a metal sensor are sensitivity and selectivity.
The sensitivity of a metal sensor is a measure of its ability to detect the reaction of a metallic object to the alternating electromagnetic field it generates. This feedback is based on eddy currents that the alternating field generated by the sensor causes (induces) in conductive objects. There is a relation between the size of the conductive object and the (to be measured) retroaction. In addition, the reaction depends on the distance to the sensor surface, the strength of the field and the conductivity of the material. Simplified, this means that the sensitivity describes the size that a conductive object must have in order to generate a usable output signal.
The selectivity of a metal sensor is a measure of its ability to infer the type of metal by the reaction of a metallic object to the alternating electromagnetic field it generates. Selective metal sensors often use several (different) frequencies to generate these measurements.
Since these two basic characteristics of metal sensors are strongly anti-correlated, precise knowledge or specification of the task is essential to select the ideal sensor for a particular application.
How does it work?
If a conductive object approaches an alternating magnetic field, self-contained induction current lines are generated on the surface of the object. Since these currents, like eddies, are self-contained, they are referred to as eddy currents. These eddy currents generate a secondary magnetic field which counteracts the primary or excitation field. The measuring principle of inductive sensors is based on this reaction of the secondary field to the primary field. The primary alternating magnetic field is usually generated by injecting an alternating current into a coil. The strength of the induced eddy current in turn depends on the material, distance and size of the conducting material.
Sensors using this effect are generally referred to as inductive proximity switches. The primary function of these sensors is to switch if there is conductive (metallic) material in its proximity. Smart parameterization or circuit technology can be used to build switches that react exclusively to ferromagnetic material, for example, while others react sensitively to all metals.
Another common application area is eddy current testing, a technique that provides insights into the different properties of an object. Eddy current testing is a non-destructive testing method that can check cracks or inclusions.
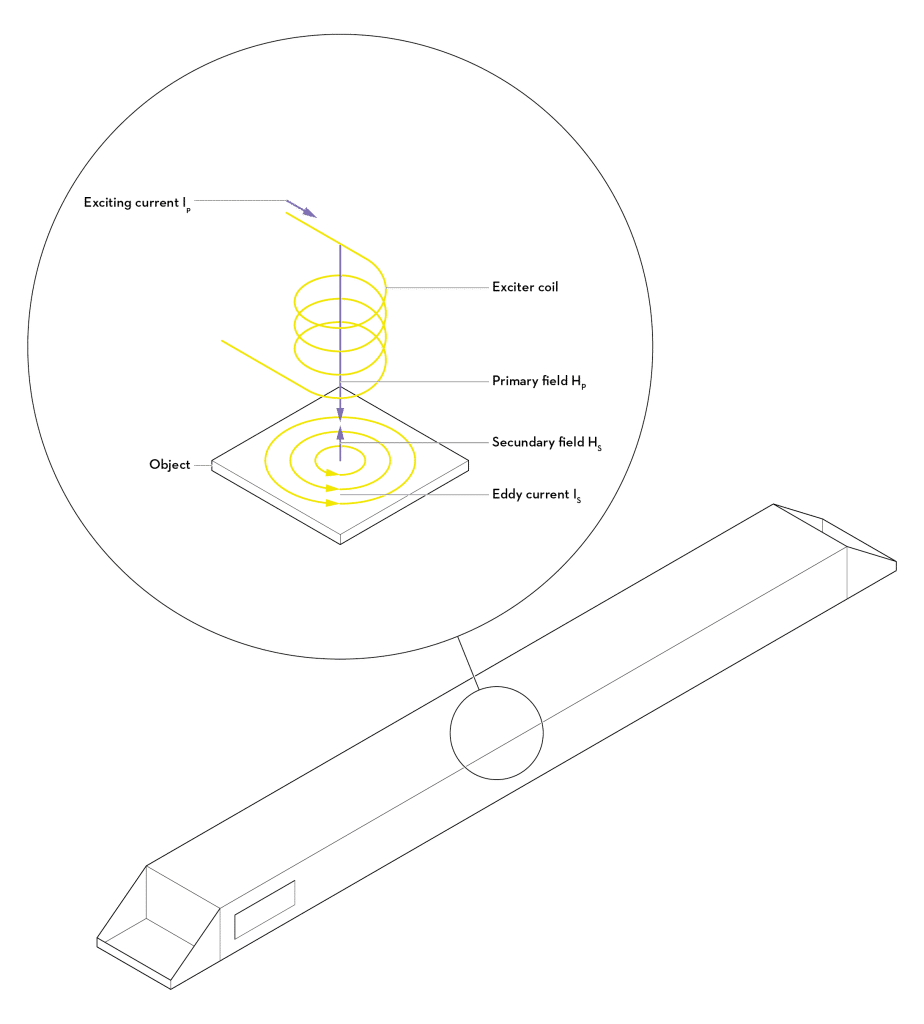
The figure shows a basic eddy current sensor. It consists of a single coil that generates an alternating magnetic field and at the same time also serves as a sensor for the reaction of any metallic object present on this field.
This system uses two receiving coils connected in such a way that a non-zero reading is provided only when a conductive object affects the primary or excitation field. This arrangement has the advantage that although disturbances affect both receiving coils, these disturbances compensate each other due to the type of interconnection.
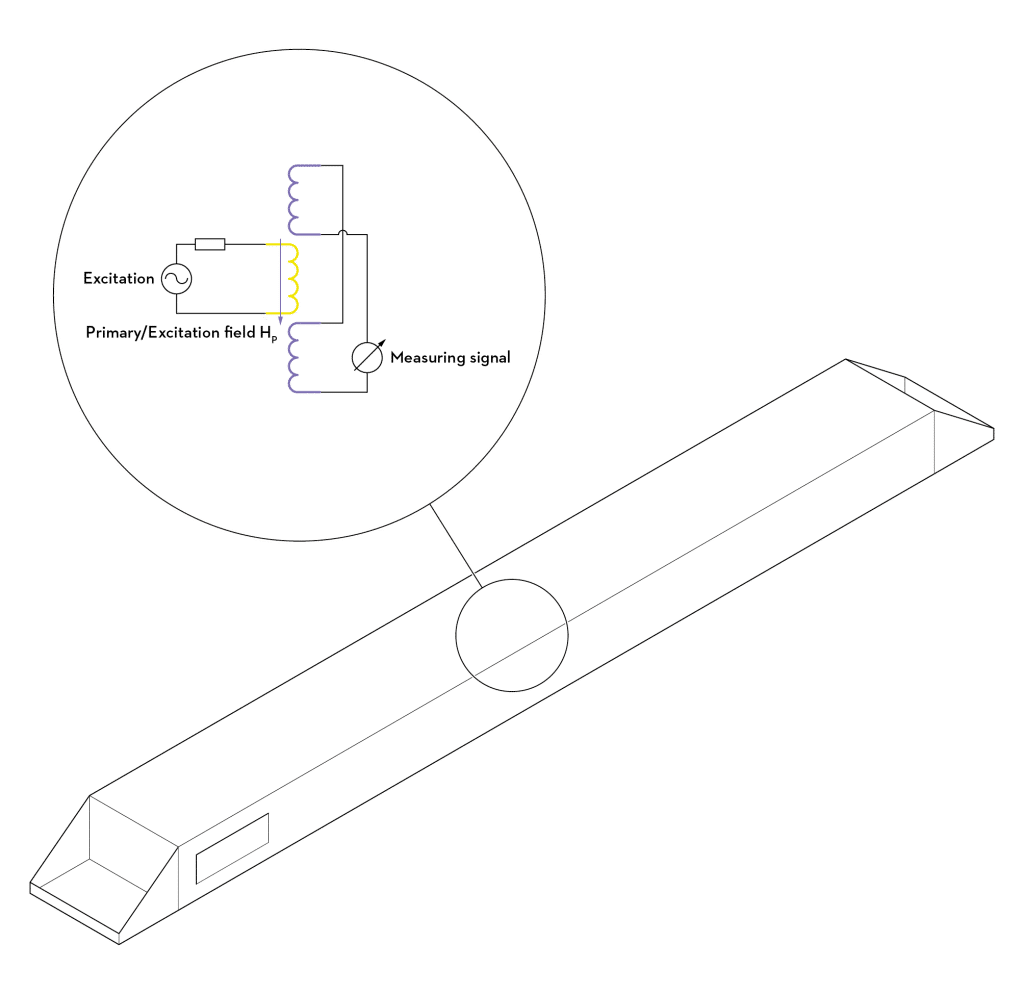
EVK products use both of these different approaches to gather information about the material passing through the sensor´s field.
You can find further articles about our technologies in our Technology Center